How To Create Your
Own Flowchart For Troubleshooting And Repairing
Purposes
Introduction
So, what is a
flowchart? According to the explanation from the Wikipedia- A
flowchart is a common type of diagram, which represents an
algorithm or process, showing the steps as boxes of various kinds,
and their order by connecting these with arrows. Flowcharts are
used in analyzing, designing, documenting or managing a process or
program in various fields.
In order for you to
easily understand what is a flowchart, just look at the sample
below:
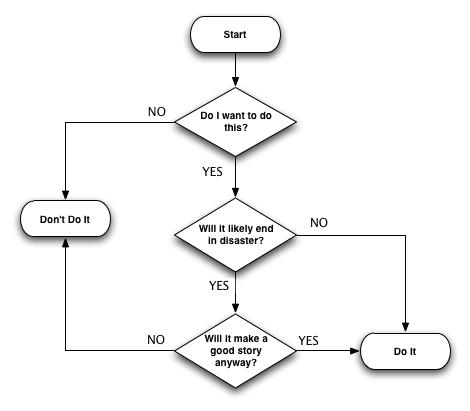
A
typical example of a flowchart
Is it necessary to
have a flowchart for troubleshooting?
If you are just
starting out in this electronic repair field, then YES it is
necessary to have this flowchart to help you out in troubleshooting
purposes. The reason is simple, since electronic equipment consists
of many circuits in it; you need a proven step by step way to be
able to locate a faulty circuit. You can’t check on ALL circuits in
the equipment as this will be a waste of time.
Let’s take this for
example, would you check on the power primary section when you
already got all the good output voltages at the secondary side of
the power supply? If you check on the power supply side, you will
be wasting your time. With a proper troubleshooting flowchart, you
will know where and
what to check so that
you will know you are on the right track of finding the bad circuit
or components.
Any ideas where I
can get the troubleshooting flowchart?
1) Service
manuals
Most of the
electronic equipment service manuals will have the troubleshooting
flowchart in the middle or at the end of the page. Do not think
that it is just another common information because I’ve seen some
of the flowchart that really consist of juicy tips in finding a
fault. Those who created the flowchart in the service manuals knew
exactly what were the common problems in the equipment. Study it
carefully and don’t miss out any good points from the
flowchart.
2)
Troubleshooting and repairing books
If you have this
kind of hard copy
books in your rack, try finding it as I believe there must be at
least some troubleshooting flowchart in some of the pages. The book
title has to be relevant to practical repair and not electronic
theories book.
3)
Internet
For your
information, there are lots of websites that offer free download on
many types of service manuals. Grab this opportunity and download
some of the service manuals and begin to do your research on this
topic.
How Does An
Electronics Troubleshooting Flowchart Look
Like?
Below is just one of
the common troubleshooting flowcharts that shows you how to tackle
faults in a CRT Monitor
Complaint-Have
high voltage but no display
An example of a more
specific flowchart
Below is just one of
the examples of a specific flowchart for a CD
player.
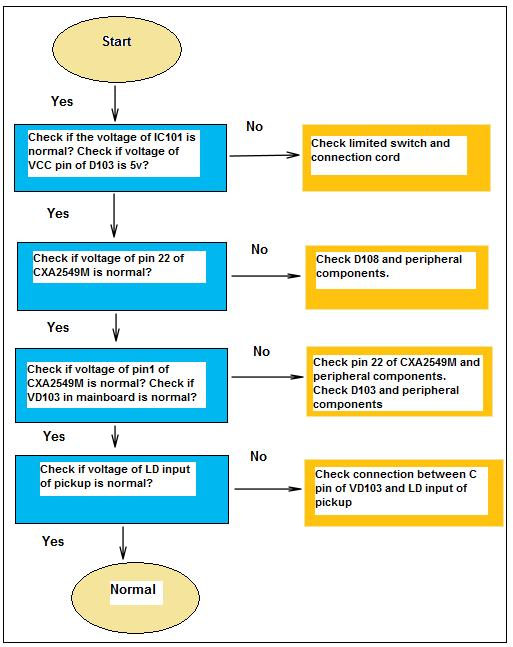
Complaint-Laser
abnormal in CD player
A specific flowchart
would usually pinpoint to a specific area like “Check that the pin
3 have output waveform” or “Check that the pin 5 of power IC I202
have 16 Vdc” and so forth.
Where to get ideas
to create the flowchart?
1) Forum and
message boards
Visit forums or
message boards that talk about the subject that is related to your
repair field. For example, if you are in LCD TV repair then visit
forum on LCD TV repair and begin to compile the solution for a
particular problem. Carefully read the posting by the professionals
and from there you could know as what you need to write in the
flowchart. Once you have created the flowchart then it would be
easy for you to follow the step by step how to solve a particular
problem.
2) From
Troubleshooting And Repairing Books or
Magazine
Some troubleshooting
and repairing books or magazine have a problem and solution
section. Gather the information posted by the author and from there
you can summarize as what you need to put in into the flowchart
boxes.
3) From you
yourself!
If you have the time
you can always create your own flowchart for reference purposes.
Think back, how you have able to solve a particular fault in
equipment. Start to draw and put in the steps that had leaded you
to find the faulty components. You may be surprised that the next
equipment that send in for repair that have similar complaint, you
could solve it in minutes with the help of a flowchart that you had
drawn.
Should I always
refer to the flowchart for every troubleshooting
job?
If possible, I want
you to memorize the flowchart so that you will be less dependent on
it. Have you ever seen any professional in electronic repair that
looks on flowchart whenever they perform a repair job? The answer
is no because they had kept all the troubleshooting procedure in
their mind and when comes to troubleshooting, they are fast in
solving a problem.
However, if you are
new in this repair field then you are required to depend on the
flowchart. Do your best to memorize it after you have created
one.
Conclusion- Create your own flowchart for your repair
industries if you are not that familiar with the equipment you are
repairing. Although it may take some of your time, I could say that
the time spent on creating your flowchart could benefits you in
days to come. If you are creative enough you can add in real photos
instead of the square/round boxes in your flowchart. Alright, this
would be my last repair article for this year and hope to see you
again next year-all the best to you!
Click here to learn how you can
become a Professional in Testing Electronic
Components
Click
here to learn how you can become a Professional in LCD
Monitor Repair
Recommendation:
Recommended Mr Kent Projection
Television Repair Membership website-Visit
Now!
Recommended Mr Kent LCD TV Repair
Membership website-Visit
Now!
Recommended Mr Kent Plasma TV
Repair Membership website-Visit
Now!
|