PART I
Interview With Steve
French-Professional Electronic Repairer From Florida
USA
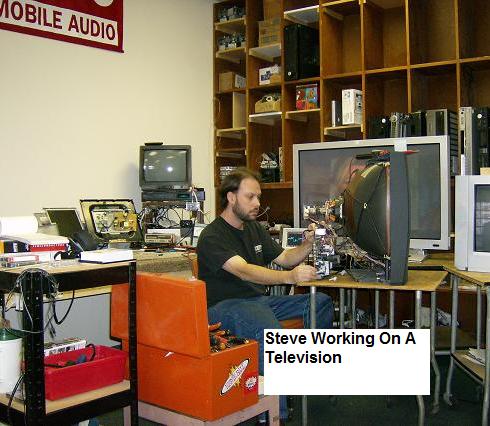
ElectronicRepairGuide (ERG)
- How long have you been in
the Electronic Repair line and at what age you own your first
repair shop?
Steve
- 18 years. I owned my first repair shop at the age of 18. I
actually got interested in electronics at a very young age though.
I was fasinated at how all those “pretty-colored” parts could do
such wonderous things. I was hooked at first
glace.
ERG
- Where is your company
located and what is the name of your company?
Steve
- I currently manage a new repair shop that just opened
in Lakeland, Florida (USA) called "Mid-Florida Electronics,
LLC". This shop is an expansion of the business
I've worked for the past 8 years. I've always run the electronic
repair department and we have grown to the point where we needed
our own storefront and repair space. And that's where we are now.
It may be a "new business" but it's far from new, only a new name
and location.
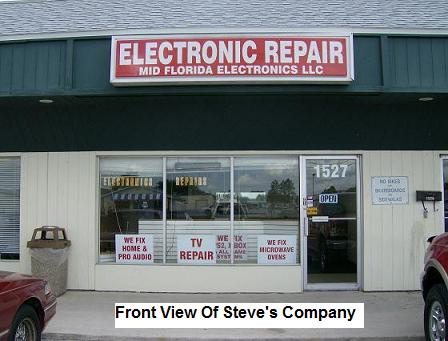
ERG
- What is your education
background?
Steve -
High school diploma is the extent of my formal studies. I took
basic electronics courses in my last three years of high school.
However, I actively work to keep up with technology and to learn
more about the things I already deal with. So, the real answer is
that my usable education is ongoing to this day. That’s the one thing we all share
as repairmen.
ERG
- Does the courses help you
in Electronic repair?
Steve -
In some ways, yes. The thing with the basic electronics classes I
took is that it taught me some basics but it didn’t teach me
anything about how to apply that knowledge to actual working
situations. I already knew most of what was taught in the courses
because I’d been studying and tinkering on my own for years
already. If I wanted to design circuits it would be a different
story. But as it was, I still had to obtain my practical knowledge
in the field, from other technicians, books and on my
own.
ERG
- Have you conduct any
electronic repair courses before? And what is the name of the
courses?
Steve -
I have taught some electronics and repair techniques to others but
never in a formal class setting.
ERG
- Do you have a
website?
Steve
- Not at the moment. Currently I’m an administrator for the website
www.tvrepairtips.org.
If you wish to join you are always welcome to do so. Our
membership is restricted, however, to people currently
working in the television (and monitor) repair business. We
have a forum and a repair tips database. A lot of our members
(such as myself) work on many types of equipment, not only
televisions.
ERG
- Which electronic repair website you frequently visited and why do
you like it?
Steve
- Tvrepairtips, of course. But I am also a member of Spyderman’s
forums for TV repair techs and I regularly read the material on and
sent out by you and some of your related sites. I feel it’s
important to be open and to learn from other repair technicians. I
love to be exposed to new ideas and methods. What better way to
improve your skills?
I’ve also learned some things from sites
like http://shelbytv.resourcez.com/
, http://noahtec.com/ , http://wa6ati.com/ , http://www.e-repair.co.uk/ and
http://www.repairfaq.org/REPAIR/
, to name a few.
ERG
- What are the Electronic
Equipment that you can repair?
Steve -
I repair practically
every type of consumer electronics. Some of the products I work on
include: TVs, home stereos, computer monitors, microwave ovens,
video game consoles, professional audio equipment, DVD players and
more.
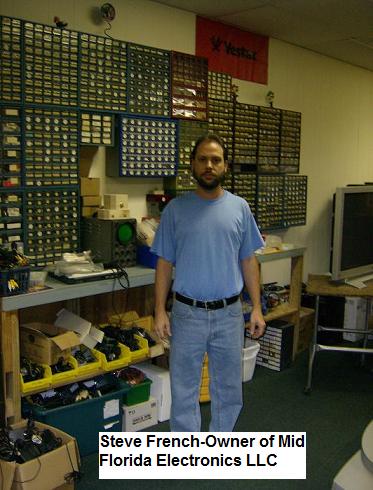
ERG
- Which type of Electronic Equipment you consider yourself expert
in?
Steve
- Probably Playstation 2 game consoles. After that, maybe microwave
ovens and home stereo equipment.
ERG
- How much time do you spend
on equipment before you give up? Why do you give
up?
Steve
- Well, Mr. Yong, that’s a hard question to a precise answer to. It
really depends on the value of the equipment. You’ve got to
consider how much you can charge for the repair to know how much
time you can realistically dedicate to any given job. For example,
I don’t mind spending 4 hours when I now the payoff may be worth
it. But if I’m working on a low priced item, such as a VCR, I just
can’t justify spending more than about 45 minutes to an hour
because I know that I can only get $20-25 to do the repair. So it’s
really a matter of value.
That being said, I still find myself
spending too much time on something every so often. Then again,
some repairs are very quick and simple so it tends to balance out
on average. But I try
to get a general idea of what’s wrong as quickly as possible. Then
I’ll give the customer an estimate that will cover the amount of
time and parts I foresee the job taking. Parts cost and
availability is a big factor when deciding how much time to spend
on something. If I find bad output ICs in a stereo receiver, I’ll
check a few preamp and power supply parts then go ahead a quote a
price. You don’t always need to find every bad part to give an
estimate, only the major parts and any others that are likely to
have failed. This can save valuable time. Especially when you feel
the price of the parts might exceed the value of the equipment and
make the customer decline the repair.
ERG
- What kind of test
equipment do you use in electronic
troubleshooting?
Steve
- My most used pieces of test equipment are: Digital multi-meter
(DMM), oscilloscope and capacitor ESR meter, but I own a large
assortment of test equipment. I feel it's important for a
technician to have and be able to use many types of test equipment.
Without the proper tools, even the most knowledgeable repairman
will be stumped far too often.
ERG
- What’s your favourite test
equipment and why do you like it?
Steve
- I love my new 200
MHZ 2 channel digital storage oscilloscope. It
gives me a lot of capabilities that I wouldn’t have otherwise. The
more types of measurements you are able to make, the better off you
are. And honestly, the beautiful color LCD screen makes me all warm
and fuzzy inside.
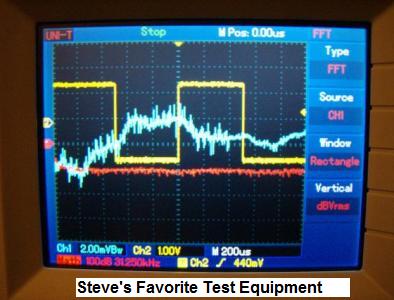
ERG
- What was the last
electronic book and magazine you read?
Steve
- I read Nuts &
Volts and Popular Electronics on a fairly regular
basis. I have a nice sized library of electronics books and
magazines that I refer to every now and then but, lately, I’ve been
re-reading the books “Using the Triggered Sweep Oscilloscope” and
“Troubleshooting with the Dual-Trace Scope”, both by Robert L.
Goodman (TAB BOOKS, Inc.).
ERG
- Generally on average how many types of electronic equipment you
can repair in a day?
Steve
- I average around 6 units a day. They tend to be an assortment of
all kinds of equipment.
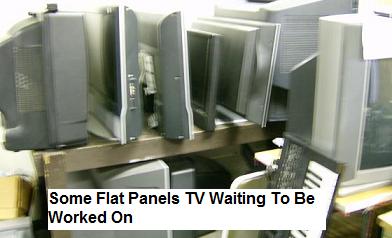
ERG
- Would you kind to share to
ERG members what are the procedures that you use in order to repair
no power symptom in a Television?
Steve
- I first perform a complete visual inspection. Are any capacitors
oozing, swollen or blown apart? Are there any bad solder
connections in the power supply, on the flyback transformer, any
heat sink-mounted components, etc? Are any components burnt? Next,
I check some major components, such as the horizontal output
transistor, fuses, and main regulator. I look for proper standby
voltages, B+ at the collector of the horizontal output transistor,
activity in the switch mode power supply and see if the
microprocessor oscillator is active. I then use the basic info I’ve
gathered to determine where to go next.
However, with all of these new flat
panel TVs and monitors out there, you’ve got to completely re-think
the way you approach troubleshooting. But in the case of a no power
condition, I also perform an ESR test on all electrolytic
capacitors in the power supply and test semiconductors for obvious
shorts. Also, it’s useful to look for the +5 VDC standby voltage at
the power/standby switch.
ERG
- Does your company have any
contracts (or appointed as an Authorized Service Centre) with any
major brands of equipment?
Steve -
We are an authorised warranty service center for a number of brands
of consumer and professional electronics brands, including
VocoPro, Mackie,
Crate and Ampeg. But there are more that we aren't
able to advertise quite yet because we're still in the process of
transferring the contracts over to the new business name. We are
also actively working on obtaining several more major name brand
warranty contracts.
Speaking of warranty contracts, I
strongly advise any shop to pursue obtaining at least a few. Not
only does that get you on the manufacturer’s referral list and gain
you access to parts and inside information but, it gets you listed
on the company’s website, in owners’ manuals, etc., meaning lots of
free advertising and new customers.
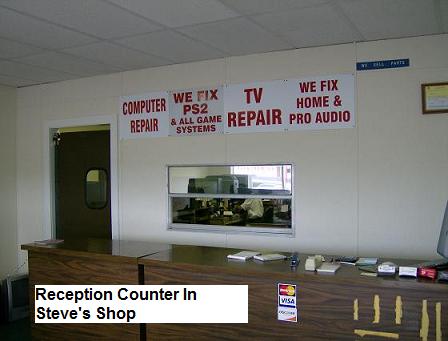
ERG -
How is your repair business
nowadays?
Steve
- We have been quite busy with both wholesale and retail
repairs.
ERG
- Do you encourage
electronic repairers to diversify into repairing more electronic
equipment-If yes then why?
Steve
- An important key to survival in today's electronics repair
business is to have the courage to try new things. If you restrict
yourself to working on only one type of product then you risk
running into a situation where you run out of work and/or miss out
on a lot of great opportunities in the repair industry. Or you get
left behind as trends and technology changes. Don't over-extend
yourself but don't pigeonhole yourself either. The more types of
equipment you can repair, the more likely you are to find something
that you really shine at, can make you money repairing and that
will keep you busy when everything else is slow. After all, we're
all in this business to make money. Fun is fun but the bills still
have to be paid.
ERG-
Do you meet regularly with
other electronic repairers to discuss about electronic problems and
solutions?
Steve
- Only on the Internet and with Don, my other technician. The sad
truth is that most technicians and repair shops view all outsiders
as the enemy. I hate that way of thinking. I can understanding not
wanting your competitors to get “too good” but it really only hurts
yourself in the long run.
ERG
- Do you do your own R &
D to find a better solution in electronic repair, for example like
coming out with your own way of solving a particular circuit
problem?
Steve
- Yes, I often do. Sometimes the answers you need are very hard to
come by or simply not available so doing your own research and
figuring out ways to troubleshoot unusual and unfamiliar systems is
a must. It also makes you a better technician in the end. I’ve even
designed and built several pieces of test equipment to help make my
job easier and the time spent was well worth it.
I’ve shared some of
my designs and test solutions on
tvrepairtips.org.
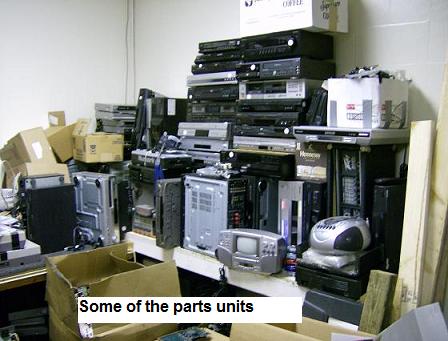
ERG
- What are the biggest
problems you are facing in the Electronic repair business
nowadays?
Steve
- That’s easy: parts and information
availability. The way I see it, we - as repair
techs - are in a constant battle against the equipment
manufacturers. We reply on fixing their equipment to make a living.
But they rely on selling new units and hate having guys like us
prolonging the life of equipment already out in customers’ homes.
As a direct result, the manufacturers are usually of little help
when it comes to service information and technical advice. And more
and more brands are nearly impossible to repair because replacement
parts are simply not available to us. The problem is that the
customers don’t always understand these things. They assume that we
have access to everything and that every TV (for example) is the
same inside. Nothing is farther from the truth. The truth is that
each and every new make and model means a challenging learning
curve for us as technicians. That’s the way it has always been and
always will be.
To make things worse, the engineers
are constantly redesigning the circuits to keep guys like us on our
toes. It’s a matter of “keep up or catch up” and both can be
difficult to do.
ERG
- Have you come across any electronic equipment that you can’t
repair? And how do you solve it?
Steve -
Absolutely! As much as I’d like to say I can fix anything, the fact
is that no one can do it all. All we can do is try our best and
apply the knowledge and resources we have in new and creative ways.
This is another case where the value of the equipment comes into
play. If I can’t narrow the problem down to the component level (or
if the parts are not available) then I’ll try to quote the customer
for replacement of the entire circuit board. Of course, I try to
avoid that but sometimes it’s the only way.
Another person with a fresh
perspective or different troubleshooting strategy might quickly
catch something that I’ve missed or didn’t even consider to be a
possible cause. So I’ll sometimes let another technician have a try
at it, either in our shop or another. We have ties to several other
shops in town. In fact, we repair a LOT of equipment for other
repair shops; they are some of our biggest accounts. So you see, if
you learn to make professional relationships you will find that
your competition doesn’t have to be the enemy. They can actually be
your greatest allies.

ERG
- How do you promote your
repair business?
Steve
- We have a radio commercial campaign going on right now. We also
rely on our signs, word of mouth, our wholesale repair accounts,
and referrals from other businesses we have ties to. We are also
listed on a number of websites for various brands as an authorised
service center.
Soon we will be starting a targeted
mailing program tochurches, bars, night clubs, hotels,
motels and restaurants. If you’re going to repair
any kind of equipment, look for places that use that equipment in
large numbers. Then you have a potential customer base to go after.
Think of all the TVs in a typical Hotel or sports
bar.
ERG
- Do you have any tips for
anyone who wants or plan to set up their own Electronic repair
shop?
Steve
- Make as many contacts as you can; You need sources for parts and
information. Don’t get in over your head with bills. I will take
time to be where you need to be (as far as income goes) so find a
storefront that you can afford. You can always grow larger as
needed. Treat your customers the way you would want to be
treated.
Spend the money and get the test
equipment you need. And finally, never stop
learning and improving your troubleshooting abilities. No matter
how good you are, you are guaranteed to become outdated if you
don’t actively keep up with technology.
And finally, one of our best moves was
to charge a non-refundable bench fee up front. Don’t underestimate
the importance of the bench fee. It’s paid when the customer leaves
the equipment and helps cover the time and some of the parts
required to give a halfway accurate estimate. Then, if they have
the unit fixed we apply the prepaid deposit towards the repair
bill.
For many years most shops in our area
gave free estimates. I was one of those. But you just can’t afford
to do that anymore. New equipment is taking more and more time to
research and diagnose and we can’t work for free. When you spend
hours just to obtain critical service information and diagnose the
problem then the customer doesn’t want to pay the price, who loses
on the deal? That’s right, the one who wasted all that time and
effort.
Some shops think they are doing the
customer a service to give free estimates. I feel that you actually
do yourself a dis-service with that strategy. Those days are gone.
If they won’t pay the bench fee you know they won’t pay the repair
bill. Doctors don’t give free diagnostics and neither do
we.
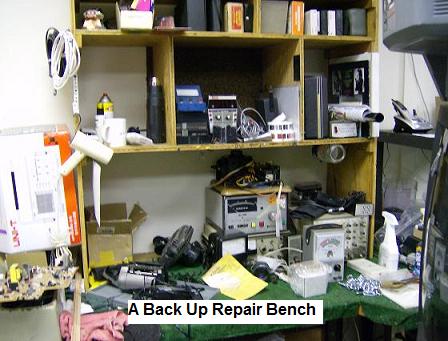
ERG
- What advice would you give
to a beginner who wish to join this trade?
Steve
- Learn to use the test equipment you've got in an efficient manner
to save yourself valuable troubleshooting time. If you can find an
easier way to narrow down the fault more quickly then it's well
worth learning to do so. Even the most basic test equipment can be
used in advanced ways if you take the time to learn
how.
But don’t forget to learn the basics,
such as electrical theory. And remember the old saying: “Your most
important test equipment is your brain.” Analytical thinking can
often take you right to the problem much faster than testing random
components. Be curious. Be safe.
ERG
- What advice would you give
to an experienced or professional electronic
repairers?
Steve
- Never stop
learning. There are plenty of books and websites -
such as Jestine Yong's network of repair sites and the one I help
administrate (www.tvrepairtips.org) - where you can expand and
share your knowledge with other repair technicians. Today's repair
world is not the same as it was 10 years ago. And the same holds
true for the future. That's why it's so important to keep actively
learning. You must work hard to keep up with modern technology
because that’s where the future is at - with or without
you.
ERG
- Did you make mistakes that
others could learn from?
Steve
- I’ve made plenty of mistakes. It goes with the territory. One
that I’ve recently learned from is to always show the customer that
their flat panel TV/monitor is working before you allow it to leave
the shop. Those things are easily damaged if they are handled
carelessly or if they fall over. If the customer cracks the screen
while moving it they may think you caused the damage. Or they may
try to blame you, knowing it was their own fault. Showing them the
unit operating will prevent you from being blamed and save you a
fortune and lots of headaches. Trust me.
ERG
- What is your future plan
for your electronic repair business?
Steve
- Our immediate plan is to become more established at our new
location and to finish setting up the new shop the way we want it.
Long-term plans include building our authorised repair status,
increasing our parts inventory, growing our customer base and
reaching the point where we need more
technicians.
ERG
- Would you kind to share your email to ERG members just in case if
they have anything related to electronic repairs to ask
you?
Steve
- mfdsteve1@verizon.net
ERG
- Thanks
Steve!
Steve
- I’d like to thank you, Mr. Yong, for all that you do for your
fellow electronic repair technicians. Thank you for allowing us
this opportunity to be featured in your article. And finally, thank
you so much for your time. Have a wonderful day.
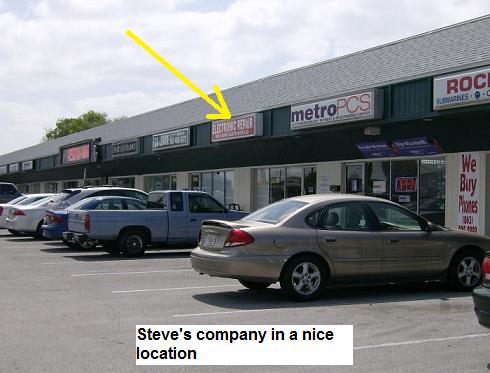
- Steve French (Manager: Mid-Florida
Electronics, LLC. 1527
S. Combee Rd. Lakeland, Florida. 33801
USA
Click Here To Go To Part
II
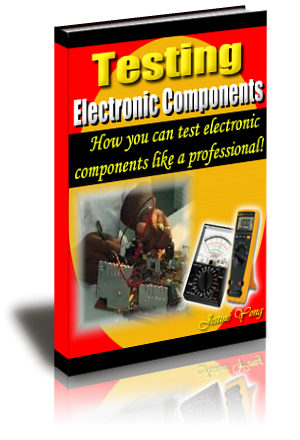
Click here to become a
professional in Testing Electronic
Components
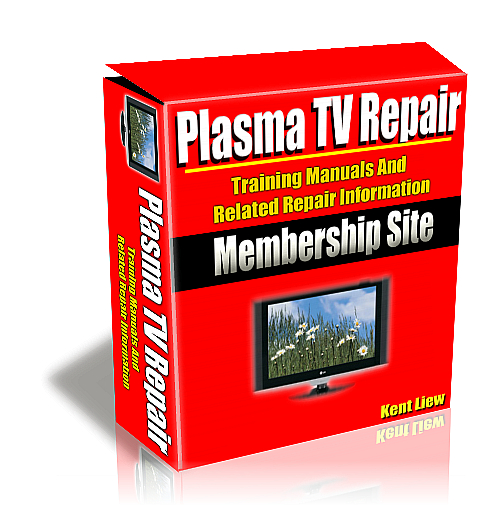
Go to part
II
|